-
Location
-
North America
-
Latin America
-
Asia Pacific
- |
- Sales & Service Partners
- |
- Contact Us
- |
-
Select Shopping Cart Account
Choose the account number for your parts ordering shopping cart. Your current cart will be saved when switching accounts.
Account# Account Name City Zip/Post Code CANCELPROCEEDMy Account
-
Industries
Industries
-
Location
-
North America
-
Latin America
-
Asia Pacific
- |
- Sales & Service Partners
- |
- Contact Us
- |
You are browsing the product catalog for
You are viewing the overview and resources for
- Blogs
- Honeywell Flying Lab Relies on ‘Golden Engine’
Your browser is not supported.
For the best experience, please access this site using the latest version of the following browsers:
By closing this window you acknowledge that your experience on this website may be degraded.
Honeywell Flying Lab Relies on ‘Golden Engine’
Aero Marketing
Honeywell’s flying testbed attracts attention wherever it flies. For starters, the modified Boeing 757 has a unique paintjob heralding Honeywell’s corporate theme, “The Future Is What We Make It,” and leading-edge company developments like connected aircraft technologies and sustainable aviation fuel.
But it’s the third engine often hung on the right side of the aircraft just behind the flight deck that draws curious stares from casual bystanders, aviation geeks and amateur photographers at airfields throughout the world, including the aircraft’s home base at Phoenix Sky Harbor.
“The primary reason we have the 757 is to help our engineers develop, test and qualify Honeywell turbofan and turboprop propulsion engines, which fly on many leading business aircraft,” said Joe Duval, Honeywell Director of Flight Test Operations. “The engineers can do lots of work in test cells on the ground, but there is no substitute for running an engine where it’s meant to be run – in the air.”
In January, the Flight Test Operations team installed a very special Honeywell HTF7000 turbofan engine on the aircraft’s third pylon for two flights critical to Honeywell’s test-flight program, according to Duval.
“We call this particular HTF7000 the ‘Golden Engine,” he said. “It’s kept in Flight Operations and we’ve been using it to correlate the data-collection system on the airplane once each year for close to 20 years. By using the same engine each year and making sure it provides the same engine data as the previous year, we can be sure that the data gathered when we test other engines is accurate and consistent.”
Test-proven engines – Honeywell’s business
Anytime an engine is tested on the 757, the onboard data-collection system gathers and records a wide range of parameters for analysis by engineers on Honeywell’s Engines & Power Systems team. Rakes and sensors in the engine measure temperature, pressure and other factors as air moves through the intake, compression, combustion and exhaust phases of jet propulsion – often called “suck, squeeze, bang and blow” inside the engine industry.
“We recently modernized the data-collection system to provide even better data for the engineering team,” Duval said. “So, the January test flights were also designed to check out those modifications to the system. That’s one of the reasons we broke this year’s Golden Engine test regimen into two four-hour flights instead of our normal flight, which lasts about six hours.”
Performance and reliability – Honeywell’s promise
“When Honeywell delivers an engine to a customer, we’re assuring them that it’s going to perform up to specifications, first time and every time,” he continued. “By using the Golden Engine to ensure our data-collection process is solid, we’re able to test engine modifications and improvements reliably and accurately. In fact, some aircraft manufacturers trust us to such a degree they limit their own development testing process.”
While engine test flights are the 757’s 'day job,' the aircraft is also used to develop, test and demonstrate Honeywell avionics, safety and communications systems. These include the company’s signature JetWave satellite communications system, IntuVue 3D weather radar, and systems that improve safety on the ground and in the air.
We inspire innovation. We are passionate and fearless inside and outside of work. We join forces and celebrate our global team. Now you can learn a little bit more about the amazing people that make up our culture at Honeywell Aerospace Technologies.
Copyright © 2025 Honeywell International Inc.
Maximum File Size
Maximum Files Exceeded
Due to inactivity you will be logged out in 000 seconds.

Maximum File Size
Maximum Files Exceeded
Your documents are ready for you. Please click here to open.
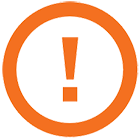
Maximum File Size
Maximum Files Exceeded
There is an issue with invoices zip file download. Please go back and try again later. Thanks!
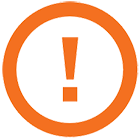
Maximum File Size
Maximum Files Exceeded
Your orders excel is ready for download. Please click here to download.
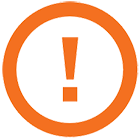
Maximum File Size
Maximum Files Exceeded
There is an issue with orders excel file download. Please go back and try again later. Thanks!
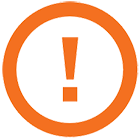