-
Location
-
North America
-
Latin America
-
Asia Pacific
- |
- Sales & Service Partners
- |
- Contact Us
- |
-
Select Shopping Cart Account
Choose the account number for your parts ordering shopping cart. Your current cart will be saved when switching accounts.
Account# Account Name City Zip/Post Code CANCELPROCEEDMy Account
-
Industries
Industries
-
Location
-
North America
-
Latin America
-
Asia Pacific
- |
- Sales & Service Partners
- |
- Contact Us
- |
You are browsing the product catalog for
You are viewing the overview and resources for
- Blogs
- 7 Ways to Improve Maintenance Costs with the Connected Aircraft
Your browser is not supported.
For the best experience, please access this site using the latest version of the following browsers:
By closing this window you acknowledge that your experience on this website may be degraded.
7 Ways to Improve Maintenance Costs with the Connected Aircraft
Kathryn Kearney
The cost of aircraft maintenance is not just the direct cost of fixing or replacing parts. The worldwide cost of flight delays, often due to maintenance issues, is over $26 billion. The cost of a grounded aircraft can be felt in passenger dissatisfaction and can affect the bottom line. As the industry matures, Honeywell Aerospace is providing new technologies for safer and smarter flights. Opening the data pipe to and from the aircraft has made it easier than ever to anticipate issues and reduce the cost of maintenance.
Here are seven ways you can improve maintenance costs with the Connected Aircraft:
1) Turn aircraft data into actionable metrics. With satellite communication, turning data into actionable metrics helps customers keep operations at optimal efficiency. Capturing and analyzing data on usage and wear enables flight crews to more efficiently inspect auxiliary power units (APUs), wheels and brakes, and environmental control systems, leading to more rapid and streamlined maintenance processes and lower costs.
2) Predict which aircraft components need maintenance or replacement before they fail. Having the ability to predict when your airplane needs repairs greatly reduces downtime and associated costs. Predictive analysis works through wireless connections to multiple mechanical systems, giving ground crews a clear view into the state of each aircraft component and system. Knowing when maintenance is needed or when a breakage is imminent helps crews address issues before they become emergencies, creating a safer and more enjoyable flight.
3) Alert crews when maintenance is needed for fast replacement delivery. Predictive analysis helps ground crews minimize maintenance cycles through advanced notice, allowing them to order the right parts at the right time. Connected Aircraft solutions such as connected data loading and connected maintenance help reduce aircraft on-ground time and costs.
4) Increase uptime via predictive maintenance and prescriptive data. With Honeywell Forge Connected Maintenance, you get more than just system health monitoring and trend analysis. The solution can predict potential failures, but also provides a greater amount of data that identifies trouble with parts down to the subcomponent level—plus information about necessary repair or replacement procedures. In this way, operators can improve their first-time-fix rate and potentially cut troubleshooting time by up to 25%, enjoy 99% prediction accuracy, see a 10% to 15% reduction in premature removals and reduce inoperative equipment by 35%. This helps significantly reduce aircraft-on-ground (AOG) time, allowing customers to get more from your aircraft and crew members.
5) Ensure that crews don’t waste time and effort on false APU removals. Honeywell’s Forge Connected Maintenance for APUs is a highly sophisticated system that provides continuous APU monitoring for our customers. As data is gathered from the unit, it is compared with benchmark information in our database, which means we can monitor the APU’s performance and stay aware when potential faults are identified—such as a line replaceable unit that is going to fail. The system notifies the airline at least three days before the failure is predicted to occur. With very specific information, maintenance teams can quickly pinpoint the problem and take care of repair or replacement before the component fails. The Honeywell Forge Connected Maintenance solution has been proven to reduce APU-related flight delays by 35%, with fewer than 1.5% false removals.
6) Reduce the need to keep spare components on hand. With the Connected Aircraft, predictive data combined with prescriptive actions can help reduce time to repair and increase aircraft uptime and availability. Minimizing the potential for surprises also means you don’t have to keep so many spare components on hand, because crews are alerted ahead of time when failures are imminent. By using our solutions, maintenance crews have been able to reduce their overall on-hand spares by an average of 10% and have also reduced overall life-cycle costs by an average of 15%.
7) Improve aircraft operations using mobile devices. With connected systems, the same data can be shared across flight planning, tracking and postflight groups. Solutions with wireless data transfer give your in-flight crew the same information as ground-based crew so that systems and departments can communicate and make decisions together. This recently enabled one European airline to manage turnarounds and reduce flight delays by 22%, while also improving on-time performance by 30%.
The power to schedule maintenance before it’s needed can significantly reduce costs and downtime. Learn how Honeywell’s Connected Aircraft can improve your aircraft’s performance while saving you more money.
Sign up to receive exclusive marketing e-communications including updates about our product offerings, special offers, news, and events.
Copyright © 2025 Honeywell International Inc.
Maximum File Size
Maximum Files Exceeded
Due to inactivity you will be logged out in 000 seconds.

Maximum File Size
Maximum Files Exceeded
Your documents are ready for you. Please click here to open.
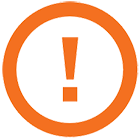
Maximum File Size
Maximum Files Exceeded
There is an issue with invoices zip file download. Please go back and try again later. Thanks!
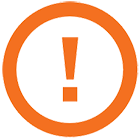
Maximum File Size
Maximum Files Exceeded
Your orders excel is ready for download. Please click here to download.
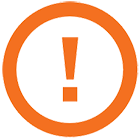
Maximum File Size
Maximum Files Exceeded
There is an issue with orders excel file download. Please go back and try again later. Thanks!
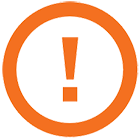