-
Location
-
North America
-
Latin America
-
Asia Pacific
- |
- Sales & Service Partners
- |
- Contact Us
- |
-
Select Shopping Cart Account
Choose the account number for your parts ordering shopping cart. Your current cart will be saved when switching accounts.
Account# Account Name City Zip/Post Code CANCELPROCEEDMy Account
-
Industries
Industries
-
Location
-
North America
-
Latin America
-
Asia Pacific
- |
- Sales & Service Partners
- |
- Contact Us
- |
You are browsing the product catalog for
You are viewing the overview and resources for
- Blogs
- Moving Beyond the Hype of Predictive Maintenance
Your browser is not supported.
For the best experience, please access this site using the latest version of the following browsers:
By closing this window you acknowledge that your experience on this website may be degraded.
Moving Beyond the Hype of Predictive Maintenance
Josh Melin
Aerospace companies have been banging the drum on predictive maintenance for a couple of decades now. The promise of a major breakthrough always seems to be just around the corner.
Nobody questions the appeal of something that will reduce unscheduled maintenance events, increase technical dispatch reliability, improve maintenance efficiency and trim operating costs. But predictive maintenance hasn’t yet lived up to the hype.
No wonder many operators are cynical about the “predictive maintenance” label. Offerings promoted as predictive maintenance tools provide vastly different levels of capability and often fall far short of delivering the implied results. In many cases, operators have had to settle for platforms that provide tons of historical data, advice on how to fix what’s already broken and trend monitoring to forecast faults.
Ideally, predictive maintenance solutions monitor onboard equipment in real time and analyze historical data. They use advanced analytics to predict which components will fail and when, so technicians can address potential issues before they can become major problems.
While they can identify a component that is likely to fail, current predictive maintenance tools aren’t able to provide much useful information about the nature of the problem. Technicians still need to go through the time-consuming process of removing, troubleshooting and repairing or replacing the faulty unit. Sometimes, they’re unable to duplicate the problem, resulting in a frustrating no-fault-found conclusion.
Even in the age of predictive maintenance, unscheduled maintenance events have big-time impact on an airline’s schedule performance, passenger satisfaction and bottom line – to the tune of $10 million-$50 million per year, by some estimates. Still, predictive maintenance has been widely viewed as the best option for airline maintenance teams.
Until now. At Honeywell we combined the capabilities of the connected aircraft and the Industrial Internet of Things to develop the aviation industry’s first true prescriptive maintenance solution. We call it Honeywell Forge for Airlines.
With Honeywell Forge, we provide maintenance teams information that can eliminate the bulk of unscheduled events by preventing faults from happening in the first place. Our breakthrough approach uses advanced predictive analytics to provide alerts of impending failures with prescribed maintenance actions. It uses cognitive diagnostics to accelerate the time to fix. And it uses connected airplane technologies to wirelessly transfer databases, software and flight data to and from the aircraft.
The Honeywell solution generates a preventive maintenance alert that can be accessed with our powerful Honeywell Forge for Airlines platform. In most cases, the alert occurs far enough in advance that the fault can be addressed during the aircraft’s next scheduled maintenance event. Cognitive diagnostics pinpoint potential problems down to the part number so that maintenance technicians know exactly which part to remove and replace to prevent an unscheduled event.
Our unique connected maintenance solution uses the latest artificial intelligence and machine learning techniques to find problems quickly and efficiently, eliminating the need for technicians to monitor and interpret data. We put actionable information at their fingertips using an intuitive mobile application, reducing the time spent troubleshooting potential problem units and speeding the process of getting key mechanical systems back on line.
In June 2018 we deployed our predictive analytics to solve top challenges facing environmental control system components. We’re currently deploying predictive analytics on wide variety of aircraft systems, including brakes and landing gear, as well as various mechanical components. We have more than two years of real-world operational experience and extensive data that proves the value of our unique solution for auxiliary power units.
Airlines using Honeywell Forge Connected Maintenance for APUs have experienced a 30-50 percent reduction in operational disruptions caused by the APU and a 10-15 percent reduction in costly premature removals. The no-fault-found rate has been reduced to 1.5 percent and the service has achieved 99 percent predictive accuracy.
Our focus so far has been the kinds of equipment that cause the highest number of delays and cancellations, as reported by the Air Transport Association. Eventually, prescriptive maintenance techniques will no doubt be used nose-to-tail, boosting efficiency throughout the airline value chain.
Copyright © 2025 Honeywell International Inc.
Maximum File Size
Maximum Files Exceeded
Due to inactivity you will be logged out in 000 seconds.

Maximum File Size
Maximum Files Exceeded
Your documents are ready for you. Please click here to open.
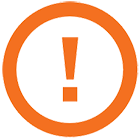
Maximum File Size
Maximum Files Exceeded
There is an issue with invoices zip file download. Please go back and try again later. Thanks!
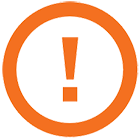
Maximum File Size
Maximum Files Exceeded
Your orders excel is ready for download. Please click here to download.
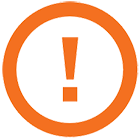
Maximum File Size
Maximum Files Exceeded
There is an issue with orders excel file download. Please go back and try again later. Thanks!
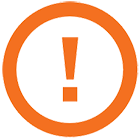