-
Location
-
North America
-
Latin America
-
Asia Pacific
- |
- Sales & Service Partners
- |
- Contact Us
- |
-
Select Shopping Cart Account
Choose the account number for your parts ordering shopping cart. Your current cart will be saved when switching accounts.
Account# Account Name City Zip/Post Code CANCELPROCEEDMy Account
-
Industries
Industries
-
Location
-
North America
-
Latin America
-
Asia Pacific
- |
- Sales & Service Partners
- |
- Contact Us
- |
You are browsing the product catalog for
You are viewing the overview and resources for
- Blogs
- Advanced Electroplating – Honeywell’s Approach for Oil and Gas Drilling
Your browser is not supported.
For the best experience, please access this site using the latest version of the following browsers:
By closing this window you acknowledge that your experience on this website may be degraded.
Advanced Electroplating – Honeywell’s Approach for Oil and Gas Drilling
Aero Marketing
Honeywell has partnered with industrial coating providers to distribute and apply its advanced electroplating technology for use in demanding conditions within the oil and gas industry. The new coating is now being field-tested by several major oil and gas companies to protect drilling tools from corrosion and abrasion.
“Coming from a demanding industry like aerospace, we understand the vigorous demands placed on essential equipment used by oil and gas companies during the exploration and development processes,” said Enrique Terrats, Senior Director of Business Development at Honeywell. Benefiting from decades of experience with coatings for aerospace applications, Honeywell advanced electroplating is designed to outperform conventional solutions like tungsten carbide coatings (HVOF-WC), which are applied using a high-velocity oxygen fuel process, and hard chrome electroplating.
HVOF-WC coatings have high hardness but are expensive, and may be prone to failure due to low impact resistance. Also, most thermal spray processes are not suitable for non-line of sight (NLOS) applications. On the other hand, hard chrome coatings are less expensive than HVOF-WC but prone to microcracks which can initiate corrosion and erosion. In addition, there are increasing environmental concerns regarding the use of chrome plating.
Honeywell’s new coating is a solution that makes sense both economically and environmentally – it enables customers to extend their drilling hours and lower total operating costs without environmental concerns. “Our coatings and the proprietary advanced electroplating process we’ve developed protect vital parts from premature failure, which can impact performance, efficiency, and cost.” Terrats pointed out.
If you would like to know more about Honeywell Advanced Electroplating, please contact us at advancedplating@honeywell.com.
We inspire innovation. We are passionate and fearless inside and outside of work. We join forces and celebrate our global team. Now you can learn a little bit more about the amazing people that make up our culture at Honeywell Aerospace Technologies.
Copyright © 2025 Honeywell International Inc.
Maximum File Size
Maximum Files Exceeded
Due to inactivity you will be logged out in 000 seconds.

Maximum File Size
Maximum Files Exceeded
Your documents are ready for you. Please click here to open.
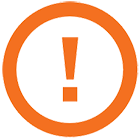
Maximum File Size
Maximum Files Exceeded
There is an issue with invoices zip file download. Please go back and try again later. Thanks!
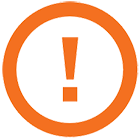
Maximum File Size
Maximum Files Exceeded
Your orders excel is ready for download. Please click here to download.
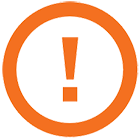
Maximum File Size
Maximum Files Exceeded
There is an issue with orders excel file download. Please go back and try again later. Thanks!
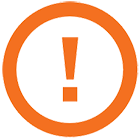