-
Location
-
North America
-
Latin America
-
Asia Pacific
- |
- Sales & Service Partners
- |
- Contact Us
- |
-
Select Shopping Cart Account
Choose the account number for your parts ordering shopping cart. Your current cart will be saved when switching accounts.
Account# Account Name City Zip/Post Code CANCELPROCEEDMy Account
-
Industries
Industries
-
Location
-
North America
-
Latin America
-
Asia Pacific
- |
- Sales & Service Partners
- |
- Contact Us
- |
You are browsing the product catalog for
You are viewing the overview and resources for
- Products
- Emerging Technologies
- High-temperature Coatings and Insulators
Your browser is not supported.
For the best experience, please access this site using the latest version of the following browsers:
By closing this window you acknowledge that your experience on this website may be degraded.
High-temperature Coatings and Insulators
Our insulators operate at up to 750°F, ensuring reliability and improved efficiency in aircraft systems.
Our high-temperature wire insulators can operate at up to 750 degrees Fahrenheit, offering increased power density and superior reliability when paired with electro-mechanical devices.
Related Categories
Copyright © 2025 Honeywell International Inc.
Maximum File Size
Maximum Files Exceeded
Due to inactivity you will be logged out in 000 seconds.

Maximum File Size
Maximum Files Exceeded
Your documents are ready for you. Please click here to open.
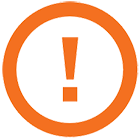
Maximum File Size
Maximum Files Exceeded
There is an issue with invoices zip file download. Please go back and try again later. Thanks!
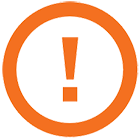
Maximum File Size
Maximum Files Exceeded
Your orders excel is ready for download. Please click here to download.
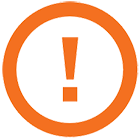
Maximum File Size
Maximum Files Exceeded
There is an issue with orders excel file download. Please go back and try again later. Thanks!
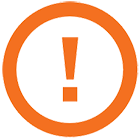