-
Location
-
North America
-
Latin America
-
Asia Pacific
- |
- Sales & Service Partners
- |
- Contact Us
- |
-
Select Shopping Cart Account
Choose the account number for your parts ordering shopping cart. Your current cart will be saved when switching accounts.
Account# Account Name City Zip/Post Code CANCELPROCEEDMy Account
-
Industries
Industries
-
Location
-
North America
-
Latin America
-
Asia Pacific
- |
- Sales & Service Partners
- |
- Contact Us
- |
You are browsing the product catalog for
You are viewing the overview and resources for
- Blogs
- Big Data Takes Flight to Improve Operations and ROI
Your browser is not supported.
For the best experience, please access this site using the latest version of the following browsers:
By closing this window you acknowledge that your experience on this website may be degraded.
Big Data Takes Flight to Improve Operations and ROI
Aerospace Marketing
Modern aircraft create vast amounts of information. Airline operators can access terabytes of data from hundreds of thousands of sources on every flight. But data is just data unless it’s used to improve operational outcomes and return on investment (ROI). That’s where advanced data analytics enter the picture.
Airlines can use big data and connected aerospace technologies to drive substantial improvements in their operations. For example, we use data analytics to predict when an aircraft part is going to fail, notifying maintenance crews of issues up to three days in advance. In Honeywell’s June 2018 Connected Aircraft Survey, airline customers identified three significant operational challenges: maintenance, fuel efficiency and turn-around time. We’re using data analytics and connectivity to address all three of these concerns.
Recently, Honeywell launched a new platform known as Honeywell Forge for Airlines. It’s an advanced analytics-based platform for airlines that helps increase profit while improving efficiency and the overall passenger experience. Data analytics changes the way that airlines handle maintenance. We’ve come a long way from the days of descriptive analytics, which essentially told the airline maintenance team that something had failed, after the fact. Predictive analytics are the standard these days, with solutions that predict what components will fail days in advance, but don’t give technicians much information about the nature of the problem or how to fix it.
Prescriptive analytics is changing the game by providing maintenance teams with this kind of information and much more. Honeywell Forge Connected Maintenance uses cognitive diagnostics, artificial intelligence and the power of the Industrial Internet of Things to alert technicians of impending failures and prescribe the best action to take to prevent them. The result is better maintenance, higher aircraft availability, fewer delays and cancelled flights, reduced turnaround time and more satisfied passengers.
To date we’ve developed more than 70 analytics models across multiple aircraft systems and types. Honeywell is the first to offer a complete nose-to-tail connected maintenance capability, covering multiple aircraft systems, which we’re getting ready to implement with a flagship customer.
Fuel efficiency has a huge impact on airlines’ bottom lines and big data is helping solve the problem. With Honeywell Forge Flight Efficiency, Honeywell gives operators information they can use to develop, implement, sustain and measure fuel-efficiency initiatives, with potential savings in the 1-3 percent range. That represents millions of dollars in savings per aircraft every year.
Honeywell Forge Flight Efficiency takes data from many different sources, on and off the aircraft, and uses advanced data analytics to help decision-makers understand how their decisions impact fuel use, schedule performance and profitability. Applying data analytics lets airlines uncover fresh ways to save fuel by impacting the three major influencers of fuel consumption: aircraft weight, engine utilization and fuel planning.
Turnaround time is another critical factor affecting airlines’ schedule performance and profitability. Once again, we applied our connectivity and data analytics expertise to create a breakthrough solution to streamline processes and manage assets at the gate and on the ramp. Honeywell Forge Ramp, lets airlines and ground service providers control the turnaround process and stay on schedule.
Honeywell Forge Ramp, provides real-time insight into the status, location and activity of aircraft and ground-based equipment at the airport. The connected ramp lets ground vehicles transmit data that can be fed into Honeywell Forge Ramp’s software, allowing users to monitor vehicle use, improve services, enhance safety and reduce turnaround time by as much as 13 percent. We recently signed a contract with Swissport, world’s largest ground service provider, after a successful proof-of-concept trial in 2018.
Sign up to receive exclusive marketing e-communications including updates about our product offerings, special offers, news, and events.
Copyright © 2025 Honeywell International Inc.
Maximum File Size
Maximum Files Exceeded
Due to inactivity you will be logged out in 000 seconds.

Maximum File Size
Maximum Files Exceeded
Your documents are ready for you. Please click here to open.
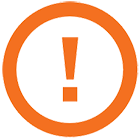
Maximum File Size
Maximum Files Exceeded
There is an issue with invoices zip file download. Please go back and try again later. Thanks!
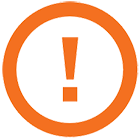
Maximum File Size
Maximum Files Exceeded
Your orders excel is ready for download. Please click here to download.
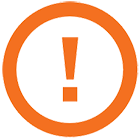
Maximum File Size
Maximum Files Exceeded
There is an issue with orders excel file download. Please go back and try again later. Thanks!
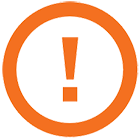