-
Location
-
North America
-
Latin America
-
Asia Pacific
- |
- Sales & Service Partners
- |
- Contact Us
- |
-
Select Shopping Cart Account
Choose the account number for your parts ordering shopping cart. Your current cart will be saved when switching accounts.
Account# Account Name City Zip/Post Code CANCELPROCEEDMy Account
-
Industries
Industries
-
Location
-
North America
-
Latin America
-
Asia Pacific
- |
- Sales & Service Partners
- |
- Contact Us
- |
You are browsing the product catalog for
You are viewing the overview and resources for
Your browser is not supported.
For the best experience, please access this site using the latest version of the following browsers:
By closing this window you acknowledge that your experience on this website may be degraded.
High-Tech Repair Solutions: Enabling Lower Total Cost of Ownership
Honeywell continues to grow our portfolio of highly specialized techniques for aircraft component repair. These advanced repairs optimize customer value through extended product life, reduced scrapping of expensive components, and lower total cost of ownership.
Our commitment to reducing maintenance spend is demonstrated by our development and delivery of cost-effective advanced repair processes. Our technology repair roadmap guides our repair development efforts to meet our customers' current and future repair requirements. With more than 230 engineers, our Global Repair and Overhaul Engineering team works to create new repairs and extended work scopes for Honeywell products. This team explores new technologies and innovative repair procedures that extend product lifespan and increase repair yield, enabling a like-new condition.
Our engineering expertise enables the ability to develop specific repairs with Original Equipment Manufacturer (OEM) reliability on Honeywell components. Our network of Global Repair Centers of Excellence supports our advanced repair techniques and presents the highest levels of engineering support and customer service no matter the repair. Through our Honeywell Operating System, Six Sigma, and Lean processes, we deliver responsive turnaround times and on-time delivery performance.
These advanced repair solutions have been proven on our industry-leading Auxiliary Power Units, TFE731, and TPE331 engine platforms, and are now being introduced to our HTF7000 platforms.
Honeywell advanced repairs include:
Adaptive Machining
Honeywell's advancements in adaptive machining systems provide comprehensive solutions for repairing and refurbishing variable-geometry 3-D components. Using the latest in 5-axis machine tools, each repair is optimized to its unique contour with minimal effect on the parent material. Honeywell uses this technology to repair impellers, blisks, and turbine rotors and blades, reducing the total cost of ownership for our customers.
Laser Welding, Brazing, and Thermal Processing
To deliver innovative repairs for the latest engine components, air cycle machines, valves, heat exchangers, and fuel control parts, while extending our work scopes for existing parts and components we push the envelope of advanced welding, heat treating, thermal sizing and high-technology brazing restoration processes. We work with new adaptive and automated laser welding technologies and brazing techniques to create high-precision repairs that are cost-effective, even for those components with complex part geometries and one-piece castings.
• 3-D Adaptive Laser Powder Fusion Welding
• Hand-held Laser System Welding
• Laser Welding, Cutting, and Drilling
• Vacuum Furnace Brazing and Heat Treatment
• Fluoride Ion Cleaning
• Electron Beam Welding
JetFix® Gas Turbine Repair Services
Honeywell's JetFix® repair services can repair severe fatigue cracks and metal erosion due to harsh engine operating environments. We use a specially formulated alloy mixture to match the original part strength. JetFix® repair service is used on turbine airfoils and includes removing the original coatings, fluoride Ion cleaning of cracks, application of the JetFix® special alloy, vacuum diffusion of the alloy, blending, recoating, and final airflow check before shipment back to the customer
Surface Treatment and Coatings
Our surface treatments and specialty coatings prevent corrosion and erosion while improving the high-temperature capability of engine parts and components. Honeywell is developing new treatment technologies and applications, including:
• Water Jet, Abrasive, and Chemical Stripping
• Thermal Spray Coatings
• CVD Aluminide Coatings
• CVD Platinum Aluminide Coatings
• EB-PVD Ceramics
• EB-PVD Metallic Coatings
Our Products
Sign up to receive exclusive marketing e-communications including updates about our product offerings, special offers, news, and events.
Copyright © 2025 Honeywell International Inc.
Maximum File Size
Maximum Files Exceeded
Due to inactivity you will be logged out in 000 seconds.

Maximum File Size
Maximum Files Exceeded
Your documents are ready for you. Please click here to open.
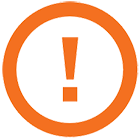
Maximum File Size
Maximum Files Exceeded
There is an issue with invoices zip file download. Please go back and try again later. Thanks!
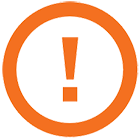
Maximum File Size
Maximum Files Exceeded
Your orders excel is ready for download. Please click here to download.
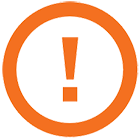
Maximum File Size
Maximum Files Exceeded
There is an issue with orders excel file download. Please go back and try again later. Thanks!
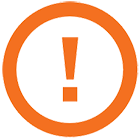