-
Location
-
North America
-
Latin America
-
Asia Pacific
- |
- Sales & Service Partners
- |
- Contact Us
- |
-
Select Shopping Cart Account
Choose the account number for your parts ordering shopping cart. Your current cart will be saved when switching accounts.
Account# Account Name City Zip/Post Code CANCELPROCEEDMy Account
-
Industries
Industries
-
Location
-
North America
-
Latin America
-
Asia Pacific
- |
- Sales & Service Partners
- |
- Contact Us
- |
You are browsing the product catalog for
You are viewing the overview and resources for
- Blogs
- Three things you need to know about additive manufacturing
Your browser is not supported.
For the best experience, please access this site using the latest version of the following browsers:
By closing this window you acknowledge that your experience on this website may be degraded.
Three things you need to know about additive manufacturing
Lauren Delafuente
Additive manufacturing is transforming the aerospace industry, unlocking numerous design possibilities and supply chain opportunities through 3D printing. Here are three things you should know about additive and why, at Honeywell, we think it can reshape the way our industry works.
Additive enables increased creativity and faster development
In the past, conventional manufacturing methods limited design creativity which ultimately limited performance. For instance, we could not easily design for a turbine blade with curved internal passageways for cooling because traditional casting methods did not readily allow for such complex shapes.
Additionally, tubes have traditionally been manufactured by welding-formed sheet metal duct work, a couple of cast or forged flanges, and perhaps a few cast bosses, into a final assembly. 3D printing can create the entire assembly as a single part number, without the added weight and multiple steps of the old manufacturing methods.
3D printing provides an unprecedented level of design freedom that enables us to create passages and shapes that can reduce weight and improve performance, unlocking tremendous value for our customers and operations.
Another benefit 3D printing brings to the table is its pace of development. Once designed using additive manufacturing, parts can be produced in a matter of days.
On the other end of the spectrum, it can take several months to make the first part of a new casting design. This is because castings require tooling, which, in turn, takes time to design and develop before the first part can be delivered. Since additive manufacturing does not require tooling, this step can be skipped altogether, which results in producing parts that can be used for initial testing in a fraction of the time. In addition, engineers can iterate to get the most optimal design quickly which saves significant cost and improves speed to market.
At Honeywell, we have a dedicated additive manufacturing design team and three high-tech labs with expert process engineers and well-trained operations staff that can get rapid prototyping done fast and right.
Additive generates supply-chain transformation
But the story doesn’t stop with rapid prototyping. Honeywell is utilizing additive manufacturing to create supply chain flexibility. Occasionally, supply-chain constraints arise. These can come from tooling or casting quality issues or simply from general spikes in demand. When Honeywell cannot deliver these parts, this impacts our customers. Additive manufacturing provides the surge capacity to respond quickly to produce parts. To enhance this capability, Honeywell has begun an aggressive campaign to qualify an additive-produced alternative to part numbers with the most significant constraints.
Equally exciting are the inventory possibilities. 3D printing can make inventory challenges a thing of the past. Instead of procuring hundreds of SKUs, then warehousing, securing, tracking and insuring them, additive manufacturing requires you only store a handful of powders, and print what you need on demand.
Finally, additive can be a logistics disruptor. Once we know our production printing process, all we have to do is push play on a machine and run through post-processing to get that part. That means we could print this part anywhere in the world where we have the same printing and processing capabilities. This results in getting the part we want where we need it while minimizing inventory, storage, shipping costs or delays.
Additive facilitates strong industry partnerships
Additive manufacturing technology is rapidly evolving, and we’re leveraging our partners to help us develop new printing strategies, classify material parameters, and test out new machines.
Additive manufacturing is excellent for prototyping and going fast, but we also print real-production qualified parts flying on aircraft today. Our strategic partnership with machine manufacturers enables us to accelerate production and expand tech adoption. Now more than ever, the aviation industry needs an agile supply chain, and that is precisely what these advanced machines bring to the table in our high-tech lab in Phoenix, Arizona.
Growing our 3D printing capabilities and capacity is an ongoing goal, and one way to achieve it is by partnering with significant part manufacturers. This collaboration enables us to share lessons learned, material property information, and different strategies to build better parts.
These partnerships will help us accelerate the adoption of additive for production parts and will play an essential role as demand for additive increases and Honeywell works to meet our customers’ needs.
Copyright © 2025 Honeywell International Inc.
Maximum File Size
Maximum Files Exceeded
Due to inactivity you will be logged out in 000 seconds.

Maximum File Size
Maximum Files Exceeded
Your documents are ready for you. Please click here to open.
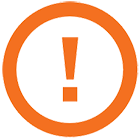
Maximum File Size
Maximum Files Exceeded
There is an issue with invoices zip file download. Please go back and try again later. Thanks!
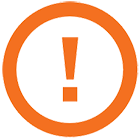
Maximum File Size
Maximum Files Exceeded
Your orders excel is ready for download. Please click here to download.
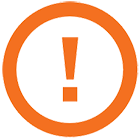
Maximum File Size
Maximum Files Exceeded
There is an issue with orders excel file download. Please go back and try again later. Thanks!
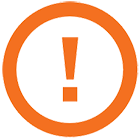