-
Location
-
North America
-
Latin America
-
Asia Pacific
- |
- Sales & Service Partners
- |
- Contact Us
- |
-
Select Shopping Cart Account
Choose the account number for your parts ordering shopping cart. Your current cart will be saved when switching accounts.
Account# Account Name City Zip/Post Code CANCELPROCEEDMy Account
-
Industries
Industries
-
Location
-
North America
-
Latin America
-
Asia Pacific
- |
- Sales & Service Partners
- |
- Contact Us
- |
You are browsing the product catalog for
You are viewing the overview and resources for
- Blogs
- How to Power a Hybrid-Electric Aircraft?
Your browser is not supported.
For the best experience, please access this site using the latest version of the following browsers:
By closing this window you acknowledge that your experience on this website may be degraded.
How to Power a Hybrid-Electric Aircraft?
Taylor Alberstadt
A few years ago, Honeywell announced its entry into the world of hybrid-electric aviation. Our first turbogenerator design combined one of our HTS-900 helicopter engines with two generators capable of powering multiple electric motors. The goal? To enable the future of flight – whether that be meeting the requirements for vertical takeoff and landing UAS/UAM vehicles, extending the range of existing airframes, or helping operators “go green.”
Since then, we’ve made great strides in our research and development, and we recently unveiled our next-generation turbogenerator, this one capable of producing a whopping 1 MegaWatt of continuous electric power. As we make these strides toward the future of flight, we receive a lot of questions from customers and the public alike. Today we’ll tackle five of the most common questions we receive.
1. What about weight? Aren’t these turbogenerators and motors extremely heavy? Wouldn’t you just put a propeller on the engine instead?
Questions about weight are the most common ones we receive any time we talk about hybrid-electric propulsion, and for good reason. Anyone in the industry knows that weight is a critically-important issue in both traditional and future aircraft. It’s true that a straight one-to-one swap doesn’t make sense for some traditional airframes. For example, there would not be significant upside to replacing a traditional Cessna Grand Caravan EX engine with a turbogenerator. However, for VTOL aimed at leveraging safety while increasing maneuverability through distributed propulsion, it can be a fantastic option. Why? Well, because it makes the aircraft not only quieter but also lighter than if mechanical power distribution were used, which is a critically-important capability for many of these designs.
Another important thing to note: Hybrid-electric power solutions are not a “one-size-fits-all” approach. It depends on the design and performance requirements, i.e., what the aircraft is intended to do. Honeywell has proprietary system tools to size the propulsion system to meet desired range targets. With the properly-sized system, the tools enable cost-benefit trades for various propulsion architectures ranging from traditional turbine engines to all-electric, and all hybrids configurations in between. Every solution we provide can be customized to a specific aircraft’s requirements. Some use a traditionally-driven propeller combined with an electric motor-driven propeller, with the engine sized appropriately to provide all power needs. Others are closer to “fully-electric” power and incorporate the use of batteries in addition to generators and motors.
2. Are hybrid-electric systems really any greener?
Another common question we receive is about how “green” this technology really is. Again, this truly depends on the specific design. If an aircraft manufacturer chooses to put a second “fuel” source in the mix (i.e., fuel cells, batteries), then yes, it’s absolutely “greener” than pure jet fuel. With multiple power sources, each can be sized to maximize performance, allowing for a smaller engine with lower fuel consumption. An example of this in the automotive world is the Toyota Prius, or any other “hybrid” vehicle.
3. Isn’t this technology untested?
Hybrid-electric technology has been thoroughly tested and proven over the course of decades. Honeywell has been building generators and turbine engines for aircraft since the 1940s. We have logged over 100 million hours of service on our engines, and they can be found on most commercial aircraft as well as helicopter platforms around the world today.
We significantly improved these same technologies and combine them in our “hybrid” systems, so the technologies themselves aren’t actually “new.” They’re merely being used in a new way.
4. Does hybrid-electric have a short shelf life? Aren’t batteries going to catch up pretty quickly?
For a variety of reasons, the assumption that turbogenerator-enabled hybrid-electric power is just “a quick stepping stone” to fully-electric designs is simply not true. It will take years, if not decades, for electrical storage to fully mature across all segments. While battery technology is promising to support propulsion needs, it has a long road to move up from Class I and II UAVs to narrow-body and wide-body commercial aircraft.
Look at the automotive industry – we’re seeing more and more electric cars, but they still have limitations when it comes to distance, terrain and infrastructure to support fast, accessible electric charging. It’s coming, but not nearly as fast as initially assumed when the first “hybrid” cars rolled off the assembly lines back in the late 1990s.
We can assume the same scenario for aircraft, and it might take even longer given the more rigorous certification requirements OEMs will face before they can take to the skies.
Furthermore, all-electric solutions may never make sense and simply won’t work for certain aircraft designs and requirements. Aircraft that need to travel further and carry heavier loads would struggle to benefit from a totally-electric design with tradeoffs between power and energy density. Additionally, aircraft that must turn around quickly between stops can’t sit and charge for extended periods of time, which for the time being is a very real concern – as many electric cars take hours to charge, not minutes and “battery-swapping” comes with similar installation and infrastructure challenges.
5. What about all those batteries onboard – are they safe?
All-electric aircraft designs require batteries; Turboelectric and Partial Turboelectric architectures don’t need them; Series, Series/Parallel, and Parallel Hybrid incorporate them in various ways. And yes, there are concerns about the safety and practicality of batteries. How do you keep them cool? What if they get too hot? What if they burst into flames?
While many companies, including Honeywell, have separate solutions to keep batteries cool when in use, this is an area where hybrid-electric power actually provides an added level of safety. In the event that batteries fail, having an alternate source of power onboard will provide a backup method of getting back to the ground safely.
Our Engines & Power Systems business unit is looking for talented Engineers passionate about the design, development, validation and certification of advanced turbomachinery products for commercial and defense applications. We are hiring across all Engineering departments and experience levels. Check out the link below to become a #futureshaper. #aerospace #hiring
Copyright © 2025 Honeywell International Inc.
Maximum File Size
Maximum Files Exceeded
Due to inactivity you will be logged out in 000 seconds.

Maximum File Size
Maximum Files Exceeded
Your documents are ready for you. Please click here to open.
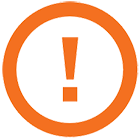
Maximum File Size
Maximum Files Exceeded
There is an issue with invoices zip file download. Please go back and try again later. Thanks!
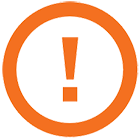
Maximum File Size
Maximum Files Exceeded
Your orders excel is ready for download. Please click here to download.
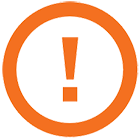
Maximum File Size
Maximum Files Exceeded
There is an issue with orders excel file download. Please go back and try again later. Thanks!
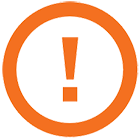