-
Location
-
North America
-
Latin America
-
Asia Pacific
- |
- Sales & Service Partners
- |
- Contact Us
- |
-
Select Shopping Cart Account
Choose the account number for your parts ordering shopping cart. Your current cart will be saved when switching accounts.
Account# Account Name City Zip/Post Code CANCELPROCEEDMy Account
-
Industries
Industries
-
Location
-
North America
-
Latin America
-
Asia Pacific
- |
- Sales & Service Partners
- |
- Contact Us
- |
You are browsing the product catalog for
You are viewing the overview and resources for
Your browser is not supported.
For the best experience, please access this site using the latest version of the following browsers:
By closing this window you acknowledge that your experience on this website may be degraded.
Honeywell produces, qualifies first valve body for military trainer jet using additive manufacturing
July 16, 2021
For the first time, Honeywell has designed, developed and qualified one of its valves using additive manufacturing, commonly known as 3D printing. The Bleed Pressure Regulating Valve is used in high temperature bleed system applications and is currently in production to be installed on the William FJ44-4M engine, which can be found on the M345 military trainer aircraft.
The valve is installed in ducting near the engine, where air coming off the engine passes through. This air is typically referred to as “bleed air.” The valve reduces the pressure of the hot bleed air to the pressure required by the environmental control system (ECS). The ECS system provides air for heating, cooling, cockpit pressurization and the oxygen generation system.
Typically, valve bodies for the FJ44-4M engine are manufactured using castings, where liquified molten metal is poured into a specially designed mold where it hardens. This process, which has been in use for hundreds of years, takes significantly more time to complete and typically produces heavier parts with unnecessary weight. In the case of this part, it is also a very casting challenging process due to the complexity of its design. Furthermore, conventional manufacturing methods like casting limit design creativity, which ultimately limits performance.
“One of the most important contributions that additive manufacturing offers is a significant reduction in the amount of time it takes to produce parts. For example, it’s helping us produce this valve body 20% faster than with typical methods, like casting,” said Tom Hart, vice president, Air & Thermal Systems, Honeywell Aerospace. “This reduction not only benefits us, but more importantly our customers. We can measure production time in days instead of months.”
Additive manufacturing provides an unprecedented level of design freedom and allows parts to be manufactured using significantly less material while still maintaining the same levels of performance. During this process, components are built from the bottom up, with layers of powdered metal fused on top of one another using a laser. This allows for rapid prototyping and helps ease supply chain constraints and shorten production time for parts.
Within this family of valves, Honeywell uses a “modular design philosophy”, which enables the same additively manufactured valve body to be used for a second valve within same aircraft bleed system. This Bleed Shut-Off Valve is used to open or shut off the supply of hot bleed air from the engine to the Pressure Regulating Valve noted above.
Full production of both the Bleed Pressure Regulating Valve and Shut-Off Valve is planned to begin later this year.
Honeywell began its efforts in metal additive manufacturing in 2007 at its lab in Phoenix. Today, the company produces hundreds of aircraft components with 3D printing and has expanded its industry-leading efforts to additional operations in China, Europe, India and the United States.
Sign up to receive exclusive marketing e-communications including updates about our product offerings, special offers, news, and events.
Copyright © 2025 Honeywell International Inc.
Maximum File Size
Maximum Files Exceeded
Due to inactivity you will be logged out in 000 seconds.

Maximum File Size
Maximum Files Exceeded
Your documents are ready for you. Please click here to open.
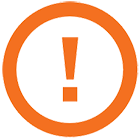
Maximum File Size
Maximum Files Exceeded
There is an issue with invoices zip file download. Please go back and try again later. Thanks!
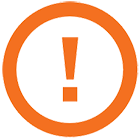
Maximum File Size
Maximum Files Exceeded
Your orders excel is ready for download. Please click here to download.
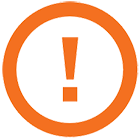
Maximum File Size
Maximum Files Exceeded
There is an issue with orders excel file download. Please go back and try again later. Thanks!
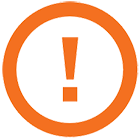