-
Location
-
North America
-
Latin America
-
Asia Pacific
- |
- Sales & Service Partners
- |
- Contact Us
- |
-
Select Shopping Cart Account
Choose the account number for your parts ordering shopping cart. Your current cart will be saved when switching accounts.
Account# Account Name City Zip/Post Code CANCELPROCEEDMy Account
-
Industries
Industries
-
Location
-
North America
-
Latin America
-
Asia Pacific
- |
- Sales & Service Partners
- |
- Contact Us
- |
You are browsing the product catalog for
You are viewing the overview and resources for
Your browser is not supported.
For the best experience, please access this site using the latest version of the following browsers:
By closing this window you acknowledge that your experience on this website may be degraded.
8 Things You Might Not Understand About Airborne Weather Radar – Part 3
Radar Corner
Stephen Hammack
March 23, 2021
Parts 1 and 2 of this series looked at some myths and misconceptions about using weather radar. In the final article of this series, we’ll close by looking at how our test group did in scenario-based evaluations using the new modes of the RDR-4000. We’ll also talk briefly about Honeywell’s latest offering, the RDR-7000.
The first set of scenario results looked at weather detection rates.
On the RDR-4000, that meant using either the AUTO mode, or ELEVATION mode (altitude slices) to detect hazardous weather and comparing it to using a manual tilt control. Compared to the manual tilt mode they had used their entire career, they scored 16.4% better looking at altitude slices and 22% better using AUTO mode.
Figure 1 – Results of scenario-based weather detection
The next set of questionslooked at weather avoidance decision making (Figure 2).
Again, we compared AUTO mode, ELEVATION mode, and conventional tilt. Compared to the manual tilt mode, they scored 33% better looking at altitude slices and 37% better using AUTO mode. Not bad for a quick 15-minute training session on the new system.
Figure 2 – Results of scenario-based avoidance decision making
The final scenario tested False Alarm rates (Figure 3).
This refers to making unnecessary deviations, wasting company time and money. You’d be surprised how many times crews deviate around islands at night in the Asia-Pacific region. Compared to the manual tilt mode they had used their entire career, they scored 17.7% better using both altitude slices and AUTO mode. Now 17% isn’t phenomenal but look at the charts again; there were no unnecessary deviations using the AUTO and ELEVATION modes compared to using manual tilt control.
Figure 3 – False alarm rates
Misconceptions About Weather Radar Usage Answered
This series looked at some misconceptions about weather radar usage and how they were addressed in the new modes of the RDR-4000. We’ll close with a quick look at why we developed a new radar. New radar designs are usually timed to match new airframes allowing OEMs to specify the interfaces, wiring, display modifications, etc. This allows any manufacturer’s radar to be dropped in on the production line. Honeywell’s RDR-4A weather radar came out with some of the first digital aircraft (B757, B767). Up to this point, air transport receiver/transmitters were 8 MCU (an ARINC form factor), weighed approximately 29 pounds, and were mounted in the forward EE-Bay to reduce the attenuation as the signal was sent to/from the antenna through a waveguide (metal rectangular pipe). Also, on widebody aircraft (A380, B777, B767, A340, etc.) there are two transmitter/receivers adding to the weight. The image was sent over an ARINC-453 interface which matched the sweep on the antenna (rho-theta format). These were all limitations imposed by the OEMs and the technology of the day. (Figure 4)
With the A380, A400M, B787, etc., it was time for a next-generation radar system. In 2002, Honeywell was awarded the contract for the A380, A400M, and C-17 Globemaster III. The A380 posed an interesting problem: Airbus wanted all the avionics in the EE-Bay (Not just the forward EE-Bay_. The sheer size of the A380, the waveguide run would have caused so much signal attenuation that there would not be enough sensitivity to provide windshear detection capability. That drove the requirements for the RDR-4000 design. The final design was a 3 MCU package, 12 pounds, and the transmitter receiver (T/R) was mounted directly on the antenna, which improved sensitivity over existing designs. The interface from the processor to the T/R was over a digital COAX cable and the display interface included legacy ARINC-453 plus high speed ethernet.
Figure 4 – Evolution of legacy radar systems to RDR-4000
Although this was a great step forward for air transport aircraft, it added an additional unit to bizjet [CA1] [KK2] aircraft which typically use an antenna, receiver, and transmitter in one unit, called an ART (Figure 5). They were able to house everything in one unit because, compared to air transport units, they were moving smaller antennas, had less features, less energy, and didn’t have the processing for features like predictive windshear.
Figure 5 – ART - Antenna/Receiver/Transmitter
With technology advances, we are now able to provide RDR-4000 functionality in the smaller ART package which includes features like windshear detection, hail and lightning prediction, and automatic weather detection and analysis modes. (Figure 6)
Figure 6 – RDR-7000 System
In future articles, we’ll explore more aspects of the IntuVue weather radar line.
Program Pilot Stephen Hammack supports Honeywell Apex and Radar for Flight Technical Services. He can be reached via email at stephen.hammack@Honeywell.com.
Copyright © 2025 Honeywell International Inc.
Maximum File Size
Maximum Files Exceeded
Due to inactivity you will be logged out in 000 seconds.

Maximum File Size
Maximum Files Exceeded
Your documents are ready for you. Please click here to open.
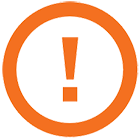
Maximum File Size
Maximum Files Exceeded
There is an issue with invoices zip file download. Please go back and try again later. Thanks!
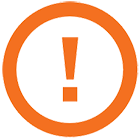
Maximum File Size
Maximum Files Exceeded
Your orders excel is ready for download. Please click here to download.
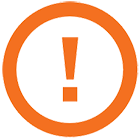
Maximum File Size
Maximum Files Exceeded
There is an issue with orders excel file download. Please go back and try again later. Thanks!
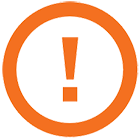