-
Location
-
North America
-
Latin America
-
Asia Pacific
- |
- Sales & Service Partners
- |
- Contact Us
- |
-
Select Shopping Cart Account
Choose the account number for your parts ordering shopping cart. Your current cart will be saved when switching accounts.
Account# Account Name City Zip/Post Code CANCELPROCEEDMy Account
-
Industries
Industries
-
Location
-
North America
-
Latin America
-
Asia Pacific
- |
- Sales & Service Partners
- |
- Contact Us
- |
You are browsing the product catalog for
You are viewing the overview and resources for
- Customer Success Stories
- Powering the Skies and Predicting the Future
Your browser is not supported.
For the best experience, please access this site using the latest version of the following browsers:
By closing this window you acknowledge that your experience on this website may be degraded.
Powering the Skies and Predicting the Future
Mechanical and software components are converging and can no longer be separate. But to merge these elements in the right way, it’s essential to bring together a historical expertise of propulsion and maintenance along with a software focus. Honeywell’s legacy experience in aircraft auxiliary power units (APUs), engines and automotive turbo chargers means that the company is distinctly positioned to do just this: strike a balance between mechanical and software expertise, so customers can continue extending the value of their aviation assets.
Now, Honeywell’s engines and APUs are already providing service reliably to more than one million people. However, keeping these mechanical components running smoothly only solves part of customers’ needs. The next level is airlines predicting issues with mechanical systems like APUs or wheels and brakes before they happen. This is where software, and connectivity come into play.
As the connected aircraft becomes a reality, the outlook of predictive maintenance will be wireless and automatic, thanks to real-time data analytics tools such as Honeywell’s IoT platform, Sentience. With Honeywell’s GoDirect Connected Maintenance, which leverages existing data links and information on our mechanical systems, we will send predictive actions to maintenance crews to address any potential mechanical issues before it causes a service disruption.
Earlier this month two early adopter airlines, Hainan Airlines and Cathay Pacific deployed Honeywell’s GoDirect Connected Maintenance service and are already seeing significant benefits.
Using existing datalinks, successful analysis of data from Cathay’s equipment showed a 35 percent reduction in operational disruptions with a false positive rate of less than one percent. With these insights, the airline is saving several hundred thousand dollars in operations and maintenance costs on a single aircraft system. All while balancing a better on-time departure schedule and comfortable travel experience for its passengers.
Meanwhile Hainan Airlines, the first airline to adopt Honeywell’s Connected Maintenance service, is equipping its current fleet of more than 50 Airbus A330s with Honeywell’s Connected Auxiliary Power Unit (APU) predictive maintenance service to improve fleet availability by identifying potential mechanical issues or failures before they happen. And this is just the tip of the iceberg.
No longer do airlines need to scramble to troubleshoot mechanical issues that take up significant time and money. Instead, they can get the data insights they need to be more efficient, to keep flights on time and passengers satisfied - an all-around win-win.
Copyright © 2025 Honeywell International Inc.
Maximum File Size
Maximum Files Exceeded
Due to inactivity you will be logged out in 000 seconds.

Maximum File Size
Maximum Files Exceeded
Your documents are ready for you. Please click here to open.
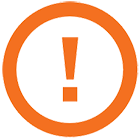
Maximum File Size
Maximum Files Exceeded
There is an issue with invoices zip file download. Please go back and try again later. Thanks!
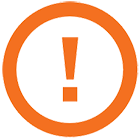
Maximum File Size
Maximum Files Exceeded
Your orders excel is ready for download. Please click here to download.
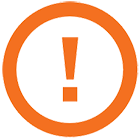
Maximum File Size
Maximum Files Exceeded
There is an issue with orders excel file download. Please go back and try again later. Thanks!
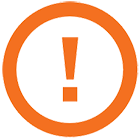