-
Location
-
North America
-
Latin America
-
Asia Pacific
- |
- Sales & Service Partners
- |
- Contact Us
- |
-
Select Shopping Cart Account
Choose the account number for your parts ordering shopping cart. Your current cart will be saved when switching accounts.
Account# Account Name City Zip/Post Code CANCELPROCEEDMy Account
-
Industries
Industries
-
Location
-
North America
-
Latin America
-
Asia Pacific
- |
- Sales & Service Partners
- |
- Contact Us
- |
You are browsing the product catalog for
You are viewing the overview and resources for
- Blogs
- What is a Gyroscope?
Your browser is not supported.
For the best experience, please access this site using the latest version of the following browsers:
By closing this window you acknowledge that your experience on this website may be degraded.
What is a Gyroscope?
Jeremy Dingman
If the word “gyroscope” still conjures up images of a gravity-defying toy balanced on the tip of a pencil, it may be time to expand your thinking.
Granted, simple gyroscopes are fun to play with and gimballed gyros are standard issue for any high school physics lab. But gyroscopes are more than kids’ toys or classroom novelties. They’re critical components of complex systems used in all kinds of aerospace, industrial and consumer applications.
Gyroscopes help navigate vehicles ranging from airplanes and ships to drones and self-driving cars. They stabilize and orient cameras, scientific instruments and robots. They isolate sensitive equipment from vibration and guide drill rigs for oil and gas producers. They’re used in virtual-reality headsets, smartphones and computer-pointing devices. They keep satellites pointed in the right direction, enabling the voice and data communications that connect our world and fuel the global economy.
Harnessing the power of the gyroscope
In its most basic form, a gyroscope is a wheel or disc, mounted on a gimbal so it can spin rapidly around an axis that is free to change direction. The angular momentum of the spinning rotor causes it to maintain its attitude even when the assembly on which it’s mounted is tilted. Gyros maintain their original orientation to a fixed point in space, unaffected by the Earth’s rotation.
French physicist Jean-Bernard-Léon Foucault is credited with inventing and naming the gyroscope in the 1850s. But it wasn’t until a half-century later that American inventor Elmer Sperry put gyroscopes to work stabilizing and navigating ships and aircraft.
Sperry developed the first practical north-seeking gyrocompass to replace less-reliable magnetic compasses on Navy ships. Soon after, he introduced the first gyrostabilizer for aircraft, which was showcased to great acclaim during a hands-off-the-controls demonstration flight during a 1914 competition in Paris. The company Sperry founded eventually became part of Honeywell, where the legacy of gyroscopic navigation, stabilization and control continues to this day.
Ushering in a new era of gyroscopic control
“Spinning iron” mechanical gyroscopes were instrumental in the aviation and naval advancements made during the first half of the 20th century. Honeywell gyroscopic systems were used throughout World War II, on applications ranging from navigation systems for aircraft, antiroll systems for ships, and stabilization systems for gunsights, bombsights and radar platforms.
The age of commercial air travel, beginning in the 1950s, was partly enabled by gyrocompasses that improved the efficiency and comfort of flight over longer distances, eventually including flights over the poles where magnetic compasses are notoriously unreliable.
Mechanical gyroscopes were still a priority for Honeywell in the middle of the century and engineers worked hard to improve the performance, reliability, size and weight of gyroscopes for aerospace and defense applications. At the same time, the company had its eyes fixed on the future and the potential to develop new, more accurate, more durable gyroscopic systems.
Introducing the ring laser gyroscope
Honeywell engineers began working on a revolutionary breakthrough in guidance and control in the early Sixties – an optical device called ring laser gyroscope (RLG), which entered production in 1966. Unlike mechanical gyros, RLGs use two laser beams traveling in opposite directions over a ring-shaped path defined by three mirrors. The gyro measures the frequency difference between the two beams to define angular velocity, which helps determine the direction that the aircraft or other platform is headed.
Unlike mechanical gyros, RLGs have no moving parts to cause friction, which can affect accuracy and increase “drift” over time. In fact, compared to a mechanical gyro that can drift 0.1-0.01 degrees per hour, an RLG drifts about 0.0035 degrees. Their accuracy, reliability and compact size make RLGs ideal for integration in modern inertial navigation systems that use gyros, computers and accelerometers to calculate the position of an aircraft, ship or other vehicle, even in the absence of GPS signals.
Despite the introduction of other technologies, such as fiber optic gyroscopes, the RLG remains the overwhelming choice for aerospace and industrial applications. Honeywell’s navigation sensors team produced its 500,000th RLG in 2019.
Taking gyros to the frontiers of space
Gyroscopes also had a few other-worldly experiences in the 1960s as Honeywell contributed various systems, including the stabilization and control system, for the Apollo 11 moon mission.
While parts of Honeywell focused on making gyros smaller, the company also pioneered development of large control moment gyros (CMGs) to stabilize and orient satellites and other spacecraft. A CMG consists of a spinning rotor and one or more motorized gimbals that tilt the rotor’s angular momentum. As the rotor tilts, the changing angular momentum causes a gyroscopic torque that rotates the spacecraft.
Honeywell hosts of the U.S. Center of Excellence for CMGs and has provided products used on hundreds of satellites and exploratory missions, as well as the international space station.
Hosting gyroscopes on an integrated circuit
Microelectromechanical system (MEMS) technologies have enabled a new generation of MEMS gyroscopes, designed to meet designers demands for ever-smaller gyros that can be mass-produced quickly and inexpensively. When the MEMS is rotated, a small mass shifts, producing a signal that can be amplified and read by a microcontroller.
You’ll find these tiny devices in smartphones, computers, medical devices and many other applications. MEMS gyroscopes are also used in automotive roll-over prevention and airbag systems, image stabilization, and have many other potential applications.
While other companies produce MEMS by the millions for commercial and consumer products, Honeywell concentrates on the high-performance systems typically used in aerospace, defense and transportation applications, including aircraft navigation systems like the attitude and heading reference system (AHRS) for commercial aircraft. The MEMS inertial measurement unit (IMU) improves the performance and accuracy of onboard navigation systems because it doesn’t require a GPS signal.
Scoping the future of gyroscopic control
The gyroscope started in 19th-century Paris as a parlor amusement and plaything. Eventually, technologies with this amazing device at their core made it to the moon and beyond and found their way into thousands of devices that touch our lives every day.
Honeywell engineers are focused on making the next generation of gyroscopic products even better, because no one knows where they’ll end up next.
For more information or to learn more about Honeywell’s GG1320, please click here.
Jeremy Dingman is the Director of Product Marketing and has been with Honeywell since 2015.
Copyright © 2025 Honeywell International Inc.
Maximum File Size
Maximum Files Exceeded
Due to inactivity you will be logged out in 000 seconds.

Maximum File Size
Maximum Files Exceeded
Your documents are ready for you. Please click here to open.
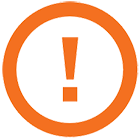
Maximum File Size
Maximum Files Exceeded
There is an issue with invoices zip file download. Please go back and try again later. Thanks!
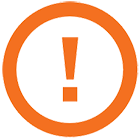
Maximum File Size
Maximum Files Exceeded
Your orders excel is ready for download. Please click here to download.
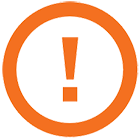
Maximum File Size
Maximum Files Exceeded
There is an issue with orders excel file download. Please go back and try again later. Thanks!
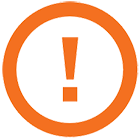