-
Location
-
North America
-
Latin America
-
Asia Pacific
- |
- Sales & Service Partners
- |
- Contact Us
- |
-
Select Shopping Cart Account
Choose the account number for your parts ordering shopping cart. Your current cart will be saved when switching accounts.
Account# Account Name City Zip/Post Code CANCELPROCEEDMy Account
-
Industries
Industries
-
Location
-
North America
-
Latin America
-
Asia Pacific
- |
- Sales & Service Partners
- |
- Contact Us
- |
You are browsing the product catalog for
You are viewing the overview and resources for
- Blogs
- Understanding reaction wheels
Your browser is not supported.
For the best experience, please access this site using the latest version of the following browsers:
By closing this window you acknowledge that your experience on this website may be degraded.
Understanding reaction wheels
Andreea Bitar
Reaction wheels are an integral part of any type of satellite and spacecraft that secure three-axis attitude control without the need of external sources of torque, like rockets or propellants. They are becoming increasingly relevant in today’s space industry because they deliver a safer, more agile and lightweight option for precision control for space systems.
Understanding how reaction wheels work and how they can benefit your operations is essential for improved performance of satellites and spacecraft.
What are reaction wheels and how do they work?
Reaction wheels are essentially flywheels that enable repositioning of controllable space vehicles and satellites while they are in orbit. A flywheel is a device that contains rotational energy, stored by conserving angular momentum, and can trigger momentum exchange to provide stability to spacecraft or satellite.
They can be used to control the position and attitude of a satellite without requiring thrusters or any other external applicators of torque. This brings multiple benefits, including a significant reduction in the payload fraction needed for fuel.
In addition, they are extremely accurate and can enable precise repositioning, which is crucial in the space industry, especially when it comes to satellite orientation.
Reaction wheels are sometimes referred to as momentum wheels because they can be operated as such, providing consistent angular momentum to a satellite, at a constant or partially constant rotation speed. Using reaction wheels as momentum wheels for angular momentum helps stabilize the satellite or spacecraft axis to point in a determined direction and is called a momentum-bias stabilization approach.
The action mechanism of reaction wheels is straightforward: a simple demonstration ca be done with a single flywheel, which is attached to an electric motor that will be integrated in a spacecraft or satellite. The object, whether spacecraft or satellite, can be subjected to external torque from different sources, such as solar radiation pressure or Low Earth Orbit (LEO) aerodynamic forces, that may come in conflict with the object’s position and attitude. As soon as the rotation speed of the spacecraft changes, the RW triggers a counter-rotation of the spacecraft, in same ratio, through conservation of the angular momentum.
This repositioning can only occur in torque; reaction wheels cannot move the spacecraft or satellite from one place to another because the total angular momentum needs to be conserved. Another aspect to consider is that the counter-rotation of the object happens along a single axis, which is why, in order to have complete control over the system, three RWs need to be deployed. In this sense, reaction wheel assemblies are the preferred choice.
Benefits of reaction wheels over thrusters
As mentioned before, reaction wheels do not require external applicators of torque and can secure three-axis attitude control autonomously. This is key advantage to a reaction wheel assembly as it saves valuable space and makes the satellite/spacecraft more lightweight and easier to manage.
Moreover, RWs can manage a satellite’s or spacecraft’s orientation with superior precision. This is a critical element for space missions of both action and observation that require very high pointing accuracy, which can be provided by satellite reaction wheels or spacecraft reaction wheels. For instance, remote sensing technology applications, such as Earth Observation (EO) satellites, could not perform at top standards without a reaction wheel assembly. EO satellites are crucial for delivering information about our planet’s environment, signaling changes that can occur and affect the Earth’s physical, biological and chemical systems. Precisely, EO satellites provide essential data on weather forecasting, natural disasters, biodiversity and wildlife trends, climate change and so on.
When it comes to reaction wheels versus thrusters, it is important to take into account the fact that thrusters are dependent on fuel, whereas reaction wheels are not. The simple switch to reaction wheels can help save costs, avoid any propellant issues that may impose safety risks and optimize accuracy.
It is also important to take a number of key factors in consideration when selecting a reaction wheel assembly. Performance and safety criteria, such as size and weight, attitude control sensitivity and precision, redundancy system, flight heritage and technology readiness level, should be among the top aspects to factor in when purchasing reaction wheels.
Honeywell is advancing the state-of-the-art for a smallsat Reaction Wheel Assembly (RWA) application by offering a technical solution that preserves Honeywell high value, heritage and reliable operation.
The Honeywell reaction wheels have been designed to offer extreme flexibility in packaging options as well as providing precision performance supported by advanced drive technology, in a greatly reduced package.
Reliability does not need to be compromised for a small scale RWA response in a large market demand.
Honeywell’s reaction wheels guarantee:
- High output, low jitter performance for precision position and pointing control
- Plug and play ACS insertion
- Minimized vehicle integration time
- Application scalable optimization
In addition, the RWA comes with key integrated Honeywell technologies, among which:
- Proven spin bearing design
- Insensitive to low or transitional operational speeds
- Optimized momentum density packaging through high speed operation
- Flexible vehicle digital interface
Sign up to receive exclusive marketing e-communications including updates about our product offerings, special offers, news, and events.
Copyright © 2025 Honeywell International Inc.
Maximum File Size
Maximum Files Exceeded
Due to inactivity you will be logged out in 000 seconds.

Maximum File Size
Maximum Files Exceeded
Your documents are ready for you. Please click here to open.
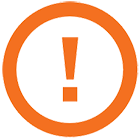
Maximum File Size
Maximum Files Exceeded
There is an issue with invoices zip file download. Please go back and try again later. Thanks!
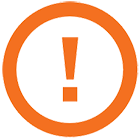
Maximum File Size
Maximum Files Exceeded
Your orders excel is ready for download. Please click here to download.
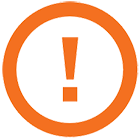
Maximum File Size
Maximum Files Exceeded
There is an issue with orders excel file download. Please go back and try again later. Thanks!
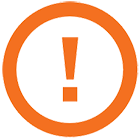