-
Location
-
North America
-
Latin America
-
Asia Pacific
- |
- Sales & Service Partners
- |
- Contact Us
- |
-
Select Shopping Cart Account
Choose the account number for your parts ordering shopping cart. Your current cart will be saved when switching accounts.
Account# Account Name City Zip/Post Code CANCELPROCEEDMy Account
-
Industries
Industries
-
Location
-
North America
-
Latin America
-
Asia Pacific
- |
- Sales & Service Partners
- |
- Contact Us
- |
You are browsing the product catalog for
You are viewing the overview and resources for
Your browser is not supported.
For the best experience, please access this site using the latest version of the following browsers:
By closing this window you acknowledge that your experience on this website may be degraded.
Share Space on Wafers for Rad-Hard Chip Designs
Honeywell adds multi-project wafer (MPW) runs to dedicated rad-hard foundry services
Aero Marketing
Your missions are extremely critical, the electronics must be of the highest reliability, and minimizing risk is a top priority.
Satellites, spacecraft and all the equipment they carry need to be designed to survive and function normally under extreme conditions and for the lifespan of the mission. They must withstand sudden vibration, extreme temperature fluctuations and high electrostatic discharges. But the most disruptive force for electronic components on satellites and spacecraft is radiation.
Exposure to radiation wreaks havoc on electronic components, causing them to malfunction or fail. Designers need to correctly handle the radiation hardness of components in order for a craft to operate flawlessly over a mission lifetime. That’s why engineers designing space-grade microelectronics specify radiation-hardened ASICs (Application Specific Integrated Circuits) for their projects.
Beyond space applications, rad-hard components also are necessary for mission-critical military applications like ships, aircraft, and land vehicles that would be expected to operate through the effects of man-made nuclear events.
Further complicating matters—shrinking device sizes make radiation hardening even more complex and costly. Designers need more cost-effective ways to get ever-smaller, rad-tolerant parts into their systems.
Making Rad-hard ASICs More Accessible
Although there are several microelectronics manufacturers able to produce components appropriate for some spacecraft and missions, few foundries are able to produce ASICs able to withstand long-duration exposure to intense radiation, or exposure to weapons-grade radiation.
Commercial foundries do not have the wafer technology and associated controls required for space-worthy microelectronics. Dedicated radiation-hardened foundry services have these controls.
Honeywell is one of the only dedicated radiation-hardened foundries to make ASICs that can tolerate extreme radiation levels. The Honeywell silicon on insulator (SOI) complementary metal oxide semiconductor (CMOS) foundry is the foundation for manufacturing integrated circuits. Implementing custom designs on a radiation hardened process greatly reduces risk of failure in radiation environments, allows size reduction and increases reliability as compared to board level designs.
Today, Honeywell’s radiation-hardened SOI CMOS technology is easier to access with the addition of Multi-Project Wafer (MPW) foundry services. ASIC designers can now share wafer resources on two Honeywell process nodes: SOI4 and S150. By using the MPW service, an MPW run can reduce prototype costs up to 80% compared to a full wafer run.
Three Ways to Use Rad-hard MPW Runs
“Sharing space on a wafer makes sense to prototype and produce designs in low quantities. A customer can evaluate high performance sections of a design, a single full design or multiple designs. MPW runs allow designers to explore the benefits of rad-hard technology without committing to large-volume wafer starts,” Thomas Romanko, Principal Application/Systems Sales Engineer, Honeywell Aerospace.
Prototyping next-gen chips. MPW greatly reduces prototype costs of next-gen chips and allows designers to test critical circuits in different versions to determine which will best meet needs.
Research or early development projects. Developing a proof-of-concept requires a large amount of design resources. Rad-hard MPW runs alleviate some of these costs for microelectronic designers.
Design adjustments. Designers can more economically test different circuit adjustments to see which one works before you commit to a final design.
Honeywell Multi-Project Wafer Foundry Services
The ability to produce chip designs in lower quantities and at lower costs opens the door for more innovation in radiation-prone environments like space and defense. Honeywell has over 30 years’ experience delivering products for extreme radiation environments. We are a Defense Microelectronics Activity (DMEA) Category 1A accredited Trusted Foundry supplier. We have been serving the Department of Defense (DoD) needs for secure microelectronics for decades.
Learn more about our rad-hard foundry services.
Copyright © 2025 Honeywell International Inc.
Maximum File Size
Maximum Files Exceeded
Due to inactivity you will be logged out in 000 seconds.

Maximum File Size
Maximum Files Exceeded
Your documents are ready for you. Please click here to open.
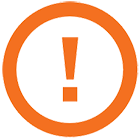
Maximum File Size
Maximum Files Exceeded
There is an issue with invoices zip file download. Please go back and try again later. Thanks!
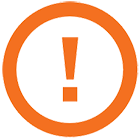
Maximum File Size
Maximum Files Exceeded
Your orders excel is ready for download. Please click here to download.
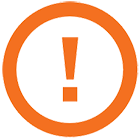
Maximum File Size
Maximum Files Exceeded
There is an issue with orders excel file download. Please go back and try again later. Thanks!
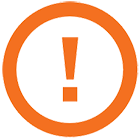