-
Location
-
North America
-
Latin America
-
Asia Pacific
- |
- Sales & Service Partners
- |
- Contact Us
- |
-
Select Shopping Cart Account
Choose the account number for your parts ordering shopping cart. Your current cart will be saved when switching accounts.
Account# Account Name City Zip/Post Code CANCELPROCEEDMy Account
-
Industries
Industries
-
Location
-
North America
-
Latin America
-
Asia Pacific
- |
- Sales & Service Partners
- |
- Contact Us
- |
You are browsing the product catalog for
You are viewing the overview and resources for
Your browser is not supported.
For the best experience, please access this site using the latest version of the following browsers:
By closing this window you acknowledge that your experience on this website may be degraded.
Honeywell Explores New Uses for Jet Engine Refractories
Alison Wyrick
April 12, 2023
Temperatures in the hot section of a turbine jet engine can reach 2000 degrees Celsius (more than 3600 degrees Fahrenheit). So, it’s no surprise Honeywell, the world’s leading producer of turbine engines for aircraft propulsion and auxiliary power, knows a thing or two about protecting vital components from extreme heat.
Honeywell is a pioneer in developing refractory materials that take heat-resistance to the next level. These same materials also are ideal for applications in industries with processes that involve extreme heat, like steel production, refining, glass manufacturing and power-generation.
Refractory Materials Protect Vital Metal Parts
Refractory materials have come a long way from the Iron Age when early humans used clay-lined kilns to smelt iron ore. The modern era of refractory materials began with the Industrial Revolution and continued into the 1900s, driven by an ever-increasing demand for steel and aluminum. The post-World War II period saw the introduction of new refractory materials and production technologies.
Today, refractory materials line the hot surfaces inside jet engines, blast furnaces, glass ovens and manufacturing equipment. They are made of nonmetal materials, usually ceramics, that can withstand temperatures well beyond the melting point of steel, around 1350°C.
Many industrial processes require refractories with mechanical and chemical stability resistance to thermal shock at 900°C and above. Oxide of aluminum (alumina), silicon (silica) and magnesium (magnesia) are some of the most important and common materials used in refractories. Silicon carbide, tungsten carbide and molybdenum disilicide also have refractory properties.
Honeywell Innovations Deliver Superior Performance
Our next-generation refractories provide new state-of-the-art solutions for aerospace and industrial companies. Zirconia (zirconium oxide or ZrO₂) can withstand ultra-high temperatures, while alumina-zirconia-carbon, combined with additive materials and advanced processing methods, excels in high-performance applications.
These advanced ceramics have proven themselves in aerospace applications, delivering superior performance and higher reliability at a fraction of the cost of comparable options. Best of all, they’re available today for use in a wide range of applications in aerospace and other industries.
Learn more about our latest advances in next-gen refractory technology by completing the form below.
Copyright © 2025 Honeywell International Inc.
Maximum File Size
Maximum Files Exceeded
Due to inactivity you will be logged out in 000 seconds.

Maximum File Size
Maximum Files Exceeded
Your documents are ready for you. Please click here to open.
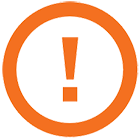
Maximum File Size
Maximum Files Exceeded
There is an issue with invoices zip file download. Please go back and try again later. Thanks!
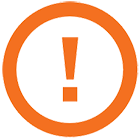
Maximum File Size
Maximum Files Exceeded
Your orders excel is ready for download. Please click here to download.
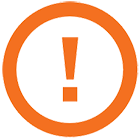
Maximum File Size
Maximum Files Exceeded
There is an issue with orders excel file download. Please go back and try again later. Thanks!
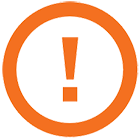