-
Location
-
North America
-
Latin America
-
Asia Pacific
- |
- Sales & Service Partners
- |
- Contact Us
- |
-
Select Shopping Cart Account
Choose the account number for your parts ordering shopping cart. Your current cart will be saved when switching accounts.
Account# Account Name City Zip/Post Code CANCELPROCEEDMy Account
-
Industries
Industries
-
Location
-
North America
-
Latin America
-
Asia Pacific
- |
- Sales & Service Partners
- |
- Contact Us
- |
You are browsing the product catalog for
You are viewing the overview and resources for
- Blogs
- Honeywell Builds on Long Legacy of MEMS Sensor Technology
Your browser is not supported.
For the best experience, please access this site using the latest version of the following browsers:
By closing this window you acknowledge that your experience on this website may be degraded.
Honeywell Builds on Long Legacy of MEMS Sensor Technology
Jeremy Dingman
You’ll find MEMS sensors just about everywhere you look these days. They sense motion to orient your smartphone screen, trigger automobile airbags, enable the use of precision medical devices and much more.
But MEMS (microelectromechanical systems) were still the new kid on the block when Honeywell acquired MEMS gyroscope and accelerometer technology from Draper in 1999 to strengthen its existing silicon micromachining capabilities.
Since then, Honeywell has applied MEMS technology to improve safety, guidance and navigation on aircraft, spacecraft, naval vessels and military land vehicles. Now the company is working on ways to use MEMS gyros and accelerometers on the latest autonomous and remotely piloted platforms, including self-driving cars, unmanned aerial vehicles and flying taxies.
Honeywell Focuses on High-Performance MEMS
While mass-produced MEMS are used in many commercial and consumer products, Honeywell focuses on the high-performance systems typically used in aerospace, defense and transportation applications, according to Senior Engineering Fellow Burgess Johnson, who’s been working on MEMS gyroscopes and accelerometers for more than two decades.
“Lots of companies make low-cost, low-performance MEMS and churn them out by the millions for use in a variety of commercial products,” Johnson said. “Our focus is on applying our depth of experience and unique end-to-end capabilities to meet the needs of customers looking for high-performing, high-quality MEMS that can function reliably under the harshest operating conditions.”
Honeywell produces MEMS for a variety of applications at its foundry in Redmond, Wash., Johnson continued. “For example, our MEMS are an integral part of aircraft navigation systems like the attitude and heading reference system (AHRS) for commercial aircraft. The MEMS inertial measurement unit (IMU) improves the performance and accuracy of onboard navigation systems because it doesn’t require a GPS signal.”
MEMS Sensors Complement GPS Nav Systems
This makes the MEMS IMU ideal for filling in the gaps when GPS signals aren’t available for whatever reason. For example, they provide precise location data when GPS signals are blocked or weak, a helicopter flies through a canyon, a submarine is under water, or a self-driving vehicle is in a tunnel or surrounded by towering buildings.
“MEMS gyroscopes and accelerometers essentially do the same thing as their mechanical ancestors,” Johnson said. “The difference is all the functions are micromachined out of a silicon wafer using equipment and techniques from the semiconductor industry. The result is a gyro or accelerometer on a chip that delivers improved performance in a smaller, lighter, lower-cost package.”
A MEMS gyro measures the Earth’s rotation against the change in rotational attitude and angular velocity of an aircraft or other moving vehicle, providing a digital output to help determine the vehicle’s direction, while a MEMS accelerometer measures the rate of change in the vehicle’s velocity.
MEMS Capabilities are Constantly Improving
“The precision of these sensors is just amazing,” Johnson said. “The error rate we achieve is less than 0.1 degrees per hour, which means we’re measuring rotation rates that are 100-200 times finer than the Earth’s rotation rate.
But Honeywell isn’t satisfied. The company continues to improve its MEMS product line, Johnson emphasized. “Right now, I’m involved in a project to improve the performance to the point where a MEMS gyro will have comparable performance to a midrange ring laser gyroscope,” he said.
Johnson said Honeywell offers a range of MEMS sensors with performance specifications to meet customers’ varying needs. “Even though we pride ourselves on providing a sensor for every application, the products we deliver often perform better than their published specifications, which makes the MEMS IMU a great sensor for the price.”
“MEMS sensors can be used whenever it’s important to accurately measure and compensate for vibration and motion,” he added. “Our products can be integrated in many kinds of platforms and many can be sold without U.S. export-control restrictions.”
Honeywell Team Focuses on Customers
Honeywell goes above and beyond to ensure that customers are choosing the right MEMS for the mission and that the units is performing up to par. Johnson noted it’s not unusual for Honeywell engineers to work directly with customers to make sure the MEMS products are meeting their needs. “I’m aware of several instances where team members have traveled to customer sites to troubleshoot problems and make sure that everything is working properly,” he said.
“We have a strong and dedicated team at Honeywell with extensive experience in these technologies. One of the things that sets us apart is that we have integrated the end-to-end process of designing, packaging, testing and manufacturing our MEMS – all at one location. This has definitely improved our efficiency and opened lines of communications so we can do a better job for our customers.”
Jeremy Dingman is the Director of Product Marketing and has been with Honeywell since 2015.
Copyright © 2025 Honeywell International Inc.
Maximum File Size
Maximum Files Exceeded
Due to inactivity you will be logged out in 000 seconds.

Maximum File Size
Maximum Files Exceeded
Your documents are ready for you. Please click here to open.
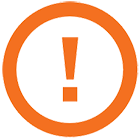
Maximum File Size
Maximum Files Exceeded
There is an issue with invoices zip file download. Please go back and try again later. Thanks!
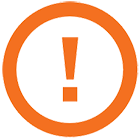
Maximum File Size
Maximum Files Exceeded
Your orders excel is ready for download. Please click here to download.
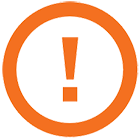
Maximum File Size
Maximum Files Exceeded
There is an issue with orders excel file download. Please go back and try again later. Thanks!
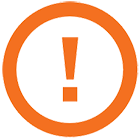