-
Location
-
North America
-
Latin America
-
Asia Pacific
- |
- Sales & Service Partners
- |
- Contact Us
- |
-
Select Shopping Cart Account
Choose the account number for your parts ordering shopping cart. Your current cart will be saved when switching accounts.
Account# Account Name City Zip/Post Code CANCELPROCEEDMy Account
-
Industries
Industries
-
Location
-
North America
-
Latin America
-
Asia Pacific
- |
- Sales & Service Partners
- |
- Contact Us
- |
You are browsing the product catalog for
You are viewing the overview and resources for
- Blogs
- Behind the scenes of an inertial sensor factory
Your browser is not supported.
For the best experience, please access this site using the latest version of the following browsers:
By closing this window you acknowledge that your experience on this website may be degraded.
Behind the scenes of an inertial sensor factory
Jennifer Strabley
We recently celebrated the shipment of our 500,000th GG1320 ring laser gyro (RLG) and I thought it would be fun to give you a behind-the-scene peek into what goes into testing their gyro before it leaves the factory.
All gyroscopes undergo rigorous performance testing and screening before they are shipped out of the factory. We also have special testing facilities that are designed to do unique performance and life monitoring. Wandering around some of Honeywell’s test facilities, you’ll see much of the test equipment oriented in the same way.
This is not for esthetic appeal, but rather because gyroscopes measure rotation -- meaning gyroscopes are able to sense earth’s rotation, some more precise than others. Earth’s rotation is nature’s perfect (and cheap!) rate table.
To test and characterize gyroscopes, we need to know where they are pointed in relation to earth’s axis of rotation through the geographic poles. If you point a gyroscope east 90 degrees to earth’s rotation, you’ll get zero output; align it to earth’s polar axis and you’ll get 15.041 degrees per hour.
So, once we’re inside a building, how do we know which direction the test stations point?
In the basement of our facility, we have a window and telescope which is used to take periodic sightings of the North Star. Using the geographic position on the earth (latitude, longitude and elevation), the time of sighting referenced to universal time coordinated (UTC) and some properties of the North Star (the right ascension and declination), we can determine the angle of the North Star and the earth’s geographic “true north.”
From there, we use what is called a “theodolite” to transfer angular information to all the test stations in the facility. Sounds complicated and it is!
Our test facility is one of just a handful of buildings worldwide that have all the critical equipment oriented correctly to the North Star. Of course, it helps that we have a few amateur astronomers amongst us to make this a bit easier!
We also care about the tilt or the degree of levelness for each test stand. Each test stand uses precision levels so that we know exactly the orientation relative to the Earth’s polar axis.
But our GG1320s are so good that we also have to care about the tilt of the floor.
Many years ago, Alan Touchberry, one of our principal system engineers, had a high-performance gyro under test and noticed a strange behavior in the gyroscope because the output was slightly unstable.
After several days of puzzling over this problem, Alan noticed a correlation with the workday and came to understand that he was seeing the effect of cars parked in the parking lot. On Monday morning cars would arrive, and, in the evening, cars would depart. Their weight made the floor tilt ever so slightly. It happened Monday through Friday, but not over the weekend.
The gyroscope under test saw the change in its orientation relative to earth’s rotation axis and faithfully reported it. This is a very small, but measurable effect with our gyroscopes. To mitigate this, our test labs are located away from the building edges and we have special stable floors decoupled from the building to prevent any sway or tilting.
So, now you know just a bit more about what it takes to manufacture 500,000 ring laser gyros! For more information about our RLGs, accelerometers, or inertial measurement units, please click here.
Copyright © 2025 Honeywell International Inc.
Maximum File Size
Maximum Files Exceeded
Due to inactivity you will be logged out in 000 seconds.

Maximum File Size
Maximum Files Exceeded
Your documents are ready for you. Please click here to open.
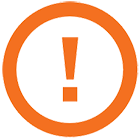
Maximum File Size
Maximum Files Exceeded
There is an issue with invoices zip file download. Please go back and try again later. Thanks!
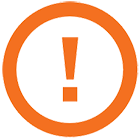
Maximum File Size
Maximum Files Exceeded
Your orders excel is ready for download. Please click here to download.
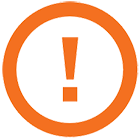
Maximum File Size
Maximum Files Exceeded
There is an issue with orders excel file download. Please go back and try again later. Thanks!
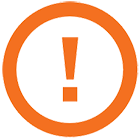