-
Location
-
North America
-
Latin America
-
Asia Pacific
- |
- Sales & Service Partners
- |
- Contact Us
- |
-
Select Shopping Cart Account
Choose the account number for your parts ordering shopping cart. Your current cart will be saved when switching accounts.
Account# Account Name City Zip/Post Code CANCELPROCEEDMy Account
-
Industries
Industries
-
Location
-
North America
-
Latin America
-
Asia Pacific
- |
- Sales & Service Partners
- |
- Contact Us
- |
You are browsing the product catalog for
You are viewing the overview and resources for
- Blogs
- Advanced Air Plasma Spray TBCs for Aerospace and Industrial Components
Your browser is not supported.
For the best experience, please access this site using the latest version of the following browsers:
By closing this window you acknowledge that your experience on this website may be degraded.
Advanced Air Plasma Spray TBCs for Aerospace and Industrial Components
Lea Kiesel
As Aerospace and Industrial Gas Turbine engines evolve, Ceramic Thermal Barrier Coatings (TBCs) must keep pace. Honeywell pioneered the use of TBCs in Aerospace in the 1980s and ’90s and has excelled in manufacturing electron-beam physical vapor deposition (EB-PVD) TBCs since the mid-2000s. While Honeywell excels in the predominant EB-PVD 6-8% yttria-stabilized zirconia (6-8 YSZ), our materials scientists and engineers have been looking to the future and the next generation of TBCs. Recent developments at Honeywell have led to a real breakthrough for Aero and IGT combustors and turbines.
After successful development and demonstration of an advanced EB-PVD TBC chemistry, the Honeywell team embarked on a multi-year effort to adapt the novel chemistry to the Air Plasma Spray (APS) process.
The Honeywell team worked to overcome many processing challenges to adapt the advanced EB-PVD chemistry into both porous and vertically-cracked TBCs. The effort resulted in a new advanced APS TBC, called “3P”.
Honeywell has performed extensive durability testing (furnace cycle testing, thermal shock testing, RT and HT erosion testing, bond cap testing, and burner rig testing) on its developed vertically-cracked and porous low-k APS TBCs. The coatings have shown equivalent or better spallation life than standard 6-8% YSZ and higher toughness than other low-k chemistries on the market. Honeywell also assessed phase stability and conductivity, using the Holloman-Jaffe parameterization technique out to 55k, and testing has shown significant advantages compared to 6-8 YSZ. Honeywell’s next-generation APS TBCs provide:
- More than 300 degrees higher phase stability
- No deleterious “monoclinic phase” even after 500 hours at 1600C.
- Up to 25% lower thermal conductivity
- Better sintering resistance.
More recent testing has shown equivalent erosion resistance compared to 6-8 YSZ, which is a considerable achievement for any advanced TBC!
With these attributes, it’s clear that this new coating has breakthrough potential. Such higher temperature capability in combination with lower conductivity at equivalent erosion resistance and spallation life can enable significant improvements in system efficiency and heat rate for IGTs and specific fuel consumption and power density for Aero engines. This can save billions of dollars in fuel and operating costs of Aero and IGT engines.
These coatings are currently being prepared for multiple engine tests for different components, including combustor liners, heat shields and burners, and turbine nozzles, blades, and shrouds. These coatings are also ready for customer field trials and full-rate production.
Visit us online to learn more about Honeywell’s expertise in thermal barrier coatings and how we can help you meet your most difficult TBC challenges.
Sign up to receive exclusive marketing e-communications including updates about our product offerings, special offers, news, and events.
Copyright © 2025 Honeywell International Inc.
Maximum File Size
Maximum Files Exceeded
Due to inactivity you will be logged out in 000 seconds.

Maximum File Size
Maximum Files Exceeded
Your documents are ready for you. Please click here to open.
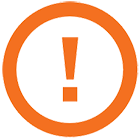
Maximum File Size
Maximum Files Exceeded
There is an issue with invoices zip file download. Please go back and try again later. Thanks!
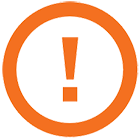
Maximum File Size
Maximum Files Exceeded
Your orders excel is ready for download. Please click here to download.
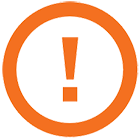
Maximum File Size
Maximum Files Exceeded
There is an issue with orders excel file download. Please go back and try again later. Thanks!
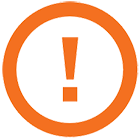