-
Location
-
North America
-
Latin America
-
Asia Pacific
- |
- Sales & Service Partners
- |
- Contact Us
- |
-
Select Shopping Cart Account
Choose the account number for your parts ordering shopping cart. Your current cart will be saved when switching accounts.
Account# Account Name City Zip/Post Code CANCELPROCEEDMy Account
-
Industries
Industries
-
Location
-
North America
-
Latin America
-
Asia Pacific
- |
- Sales & Service Partners
- |
- Contact Us
- |
You are browsing the product catalog for
You are viewing the overview and resources for
- Blogs
- 4 Ways Changes in Aircraft Design and Components Reduce Fuel Consumption
Your browser is not supported.
For the best experience, please access this site using the latest version of the following browsers:
By closing this window you acknowledge that your experience on this website may be degraded.
4 Ways Changes in Aircraft Design and Components Reduce Fuel Consumption
Kathryn Kearney
Fuel is often the single largest cost for most aircraft operators, whether military or civilian. Some experts estimate that every pound of a plane’s weight, including crew, passengers, baggage and the aircraft itself, totals up to approximately $10,000 in annual fuel costs. To reduce aircraft weight—and therefore fuel usage—design and maintenance organizations are looking at nearly every aspect of aircraft. Even small changes in these areas can add up to significant results.
Here are four ways changes in aircraft design are helping reduce fuel consumption:
Drag Reduction. Reducing the lift-to-drag ratio of an aircraft can make it more aerodynamically efficient and help reduce the aircraft’s weight and fuel use. Engineers are experimenting with innovative designs that will help reduce drag. Ideas include thicker fuselages, which increase airflow, and longer, slimmer wings. Winglets, or small surfaces that lift air vertically, are being installed to help minimize the amount of air that flows around the wingtip. A concept under development at NASA, called the “double bubble” D8, relocates the aircraft’s engine to the top of the plane toward the tail—a move that significantly decreases drag and increases fuel efficiency. Engineers say the design could reduce carbon emissions by up to 66% within two decades and result in 37% less fuel consumption than that of today’s jets.
Wiring. Wires and cables can add more than 16,000 pounds to a wide-body passenger jet. Today, aircraft engineers are researching the possibility of replacing wiring in some non-avionic systems, such as those that control cabin lighting, cabin pressure, landing gear and door sensors, with small, lightweight wireless transceivers. Using long-life batteries, the transceiver modules could be installed on components in the plane. The modules would gather and send data to router-like concentrators powered by the plane’s electrical system. Data needed by the pilot would be displayed on tablet PCs in the cockpit. Some researchers are also looking into “fly-by-wireless” systems that would replace wired connections between safety-critical avionics components, including an aircraft’s engine, navigation system and onboard computers.
New Components, Equipment Designs and Materials. New manufacturing processes have made high-performance and lightweight carbon brakes similar in cost to steel brakes. Engineers are continually striving to develop lighter-weight aircraft materials that won’t compromise strength and safety. Carbon-fiber reinforced polymers have been used since the 1970s but traditionally only in specific parts of the aircraft, such as tail components. Manufacturers are using carbon-fiber composites more extensively because they are lighter than aluminum alloys. Using carbon-fiber composites instead of metal to build wings, for instance, can cut fuel consumption by 5%.
Efficient Engines. Aviation researchers are helping reduce fuel usage by creating hybrid-electric engines and lighter-weight engines. For instance, Honeywell’s hybrid-electric turbogenerator runs partially on electricity, which results in less traditional fuel used. The propulsion system combines the HTS900 engine with two compact, high-power-density generators. Each generator delivers 200 kilowatts—when combined, that’s enough to power 40 average American homes running air conditioning at full blast. A single Honeywell turbogenerator could power multiple electric motors located anywhere on an aircraft.
With every ounce on an aircraft equating to dollars spent on fuel, it is critical that we continue to research new ways to reduce a plane’s overall weight. Less weight means less fuel used, which can add up to millions in savings. The potential savings are making weight reduction a major priority for commercial airlines, business jet owners, militaries and rescue operations, and cargo companies alike. Fortunately, advanced technology is making it easier for engineers to research and develop new opportunities.
Copyright © 2025 Honeywell International Inc.
Maximum File Size
Maximum Files Exceeded
Due to inactivity you will be logged out in 000 seconds.

Maximum File Size
Maximum Files Exceeded
Your documents are ready for you. Please click here to open.
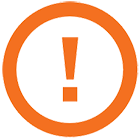
Maximum File Size
Maximum Files Exceeded
There is an issue with invoices zip file download. Please go back and try again later. Thanks!
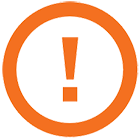
Maximum File Size
Maximum Files Exceeded
Your orders excel is ready for download. Please click here to download.
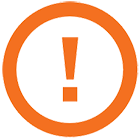
Maximum File Size
Maximum Files Exceeded
There is an issue with orders excel file download. Please go back and try again later. Thanks!
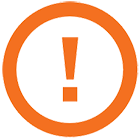